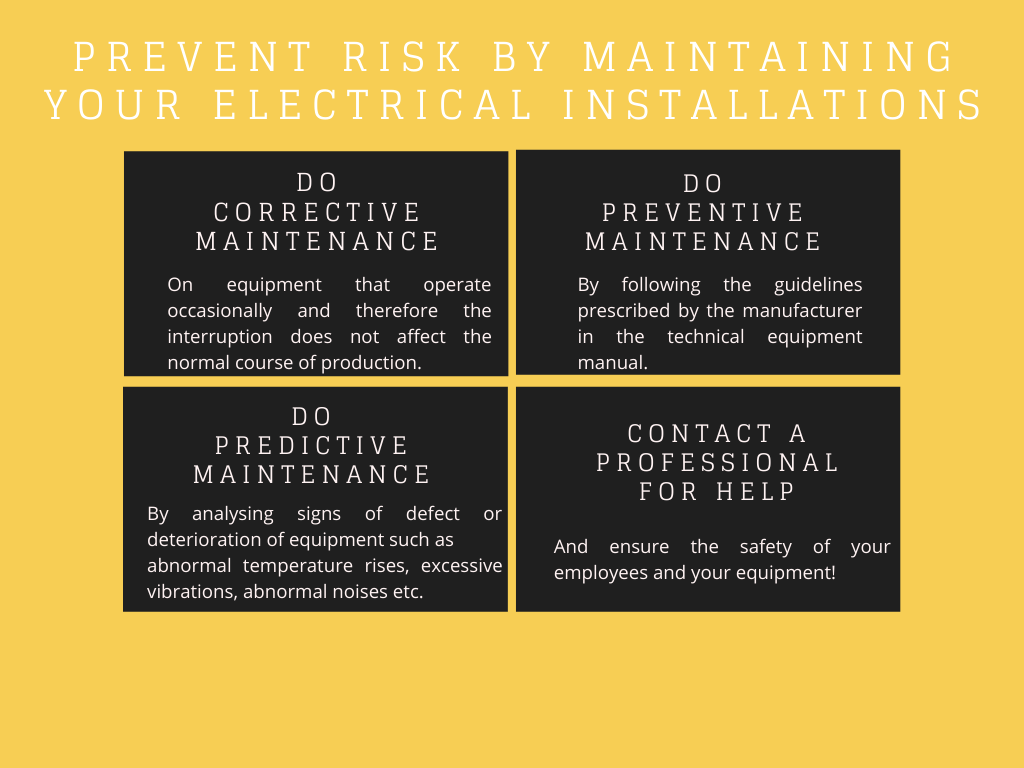
Prevent risks by maintaining your electrical installations!
The gap between the design of safe equipment and installations per the Canadian Electrical Code / Ontario Electrical Safety Code (OESC) and the acceptable safe electrical practices recommended by Electrical Safety in the Workplace is a reality. The CSA standard deals with the maintenance of electrical systems. Its purpose is to reduce this gap by providing electrical system managers with documents to help them achieve this goal. It protects workers, prevents accidents caused by electric arcs, and reduces the risk of premature electrical equipment deterioration.
There are three types of maintenance that can be carried out on electrical installations. The difference is in the resources used, the time allocated, and the equipment used to diagnose this corrective, preventive and predictive maintenance.
Corrective maintenance
We perform corrective maintenance when a problem or an anomaly has already been observed. It is more economical in the short term but can be expensive long term, especially when the equipment is old. Equipment that ages have inconsistent reliability and require fairly extensive inventory management. Its recommended to use this type of maintenance on equipment that operates occasionally, and therefore the interruption does not affect the ordinary course of the production.
Preventive maintenance
It is done following the manufacturer’s guidelines in the technical equipment manual and helps increase reliability, reduce costs, and unscheduled downtime. Other benefits seen with this type of maintenance are in the equipment’s efficiency and the increase in its useful life. It is recommended maintenance for productions with the possibility of shutdowns for scheduled work that requires diagnostic and anomaly detection devices and a lot of time to perform scheduled tasks.
Predictive maintenance
It is made based on an analysis of signs of defect or deterioration of equipment such as abnormal temperature rises, excessive vibrations, strange noises. After this analysis, maintenance is done, and time is reduced. The action is put on the essential tasks. It has the advantage of reducing costs, unscheduled shutdowns, material inventories, optimizing the equipment’s operation by increasing its efficiency and useful life. Although it has several advantages, this method also has drawbacks, which lie in the requirement to use sophisticated and expensive diagnostic equipment, the training of personnel in the use of measuring devices or the help of a professional to carry out the diagnosis favours an approach by analyzing the signs of defects (excessive vibrations, abnormal temperatures, degradation of the lubrication) before carrying out maintenance. This method reduces the time allocated for maintenance, eliminates unnecessary tasks, increases reliability, reduces costly breakdowns, reduces unplanned downtime, reduces inventory, optimizes the equipment’s operation, increases efficiency, and extends the useful life of the equipment. However, this method requires the acquisition of expensive diagnostic equipment and personnel training with the measuring devices, which is not cost-effective in the short term. This method is used for continuous production without the possibility of interruption.
The continual maintenance of our electrical equipment allows us to anticipate risks and maintain a safe working environment. It is advisable to be proactive (preventive, predictive) and non-reactive (corrective) when it comes to electrical systems because the danger is quite significant, and so is the damage.
Contact a professional now to help you with your maintenance work on your electrical systems and ensure your employees and equipment safety!
For more information, please refer to:
- Canadian Electrical Code, part I / Ontario Electrical Code
- CSA Z462 – Electrical safety in the workplace
- CSA Z463 – Maintenance of electrical systems
- https://store.csagroup.org/
Keywords:
Maintenance | Electrical installations |
Electrical safety | Corrective maintenance |
Preventive maintenance | Predictive maintenance |
Diagnosis | Electric arc |
Leave a Comment